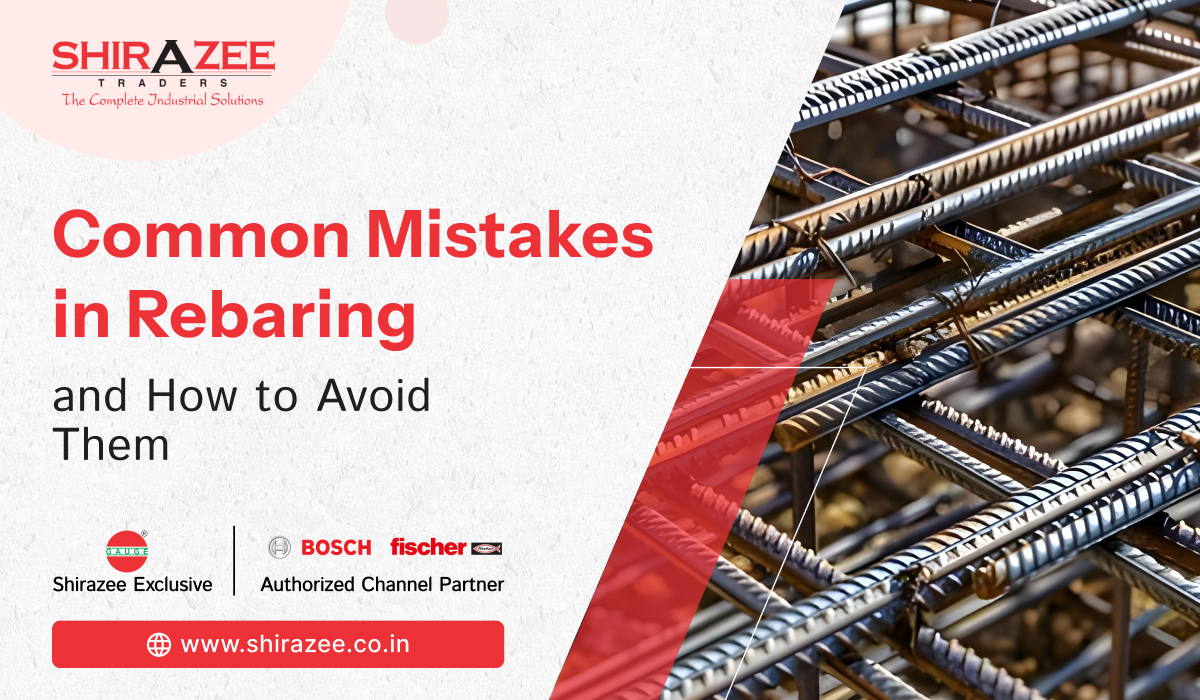
One small rebar placement mistake today can become a significant structural disaster tomorrow! If concrete is the body of a structure, rebar is the skeleton that holds it all together. Rebaring services are crucial in construction, ensuring buildings, bridges, and other structures remain strong, safe, and long-lasting. But here’s the problem—small mistakes in construction solutions can turn into massive issues.
From misplaced rebar to using poor-quality materials, these errors don’t just cost money; they compromise safety. This blog will walk you through the most common mistakes in industrial solutions related to rebaring and how to avoid them.
Because the only way to do construction correctly is to do it the first time. The placement of the rebar inside a building determines its strength, not only the concrete!
1. Incorrect Placement
Imagine spending millions on a project only to realize that misplaced rebar has weakened the entire structure! Improper placement of rebar has an impact on load distribution and structural integrity. Cracks, instability, or even collapse can result from even a small movement.
Common Mistakes:
- Misalignment or shifting during concrete pouring.
- The rebar is placed too close to the surface, making it prone to corrosion.
Example: A high-rise project had to be halted when engineers found that improperly placed rebar had made the structure vulnerable to cracks. Fixing it meant weeks of delay and skyrocketing costs.
How to Avoid It:
- Stick to engineer-approved construction solutions.
- Use rebar chairs to maintain proper positioning.
- Perform regular alignment checks before pouring concrete.
Fixing rebar placement before pouring concrete is cheap. Fixing it afterwards? A nightmare!
2. Improper Spacing
Ever hear of an early crack in a concrete structure? Rebar spacing errors are a hidden issue! Stress accumulates in specific areas if the bars are too close together or too far apart. This can cause cracks and degrade the structure.
Common Mistakes:
- Not keeping the right gap between rebar.
- Ignoring the blueprint measurements.
Example: A bridge project suffered premature cracks due to inconsistent rebar spacing. What was supposed to last decades needed repairs in just a few months!
How to Avoid It:
✔ Follow spacing guidelines in rebaring services.
✔ Conduct regular inspections before concrete pouring.
3. Poor Quality Material
Would you trust a foundation built with weak, rusted steel? Neither should your project! The quality of industrial solutions matters. Using low-grade or corroded rebar reduces a structure’s lifespan, making it prone to failure much earlier than expected.
Common Mistakes:
- Choosing cheaper, low-quality materials to cut costs.
- Using rusted or compromised rebar.
Example: A residential complex required major repairs within five years because the builders chose cheaper, lower-grade rebar. The savings upfront led to massive expenses later!
How to Avoid It:
✔ Make use of robust, corrosion-resistant rebar.
✔ Examine items prior to use.
Ignoring quality now will result in costly repairs later!
4. Inadequate Bar Bending Schedule (BBS) Preparation
One small miscalculation in the bending schedule can mess up the whole project! If the BBS isn’t right, you might run out of materials, causing delays and wasting money.
Common Mistakes:
- Poor planning leads to wasted materials.
- Wrong calculations mean running out of rebar.
Example: A commercial project was delayed by two weeks because of a mistake in BBS calculations. They ran out of rebar and had to reorder, costing more time and money.
How to Avoid It:
✔ Align BBS with structural drawings.
✔ Provide detailed BBS, including shape, size, and placement.
✔ Account for tolerances to prevent last-minute modifications.
Precision in BBS planning can save thousands in material and labour costs!
5. Lack of Coordination with Other Disciplines
What happens when rebar clashes with plumbing and electrical conduits? Chaos and rework! Poor coordination between disciplines like MEP (Mechanical, Electrical, Plumbing) and construction solutions results in conflicts, delays, and costly adjustments.
Common Mistakes:
- Not considering space for plumbing and electrical lines.
- Ignoring site coordination meetings.
Example: In a high-rise project, sections had to be redone because rebar blocked crucial electrical conduits. This unnecessary rework costs both time and money!
How to Avoid It:
✔ Check the site before placing rebar.
✔ Talk to architects and engineers to avoid clashes.
Poor coordination turns a smooth project into a messy, expensive fix!
6. Skipping Inspections
Would you drive a car without checking the brakes? Then why ignore rebar inspections? Small mistakes can grow into costly problems. Regular inspections catch errors before it’s too late.
Common Mistakes:
- Not checking rebar placement before pouring concrete.
- Skipping inspections after installation.
Example: A stadium had to undergo expensive fixes because no one checked if the rebar was correctly placed before pouring concrete. The repair bill was five times higher than what an inspection would have cost.
How to Avoid It:
✔ Implement a strict inspection process at each stage.
✔ Train workers on rebar standards and best practices.
A 10-minute inspection today can save months of costly repairs later!
7. Not Consulting Experts
Thinking you don’t need expert advice? That’s the first mistake! Even the best construction teams benefit from professional input. Ignoring structural engineers’ advice on complex projects.
Common Mistakes:
- Not listening to structural engineers on tough projects.
- Skipping proven building methods.
Example: A team ignored advice about earthquake safety. Later they found out their building wasn’t strong enough. Fixing it cost them a fortune!
How to Avoid It?
✔ You may consult with engineers for practical advice.
✔ Remain updated on industrial solutions and updated practices.
✔ Investing in expert advice to prevent massive future failures!
Summing Up!
Rebar mistakes don’t just cost money; they cost safety. Why take the risk? Every step in rebaring services matters. Safer, stronger, and longer-lasting constructions are guaranteed when the proper construction methods are followed, from precise placement to high-quality materials.
Costly mistakes can be avoided before they arise with routine inspections and professional advice. Shortcuts are not an option in the building industry. Get it correctly the first time!